Centerpoint bolts are an essential component in various industries where precision and stability are critical. They are specifically designed to be the focal point in assemblies that require exact alignment and distribution of forces. As someone with extensive experience in this field, I'm here to delve into the intrinsic value of centerpoint bolts, underlining their applications, benefits, and selection criteria to ensure optimal performance.
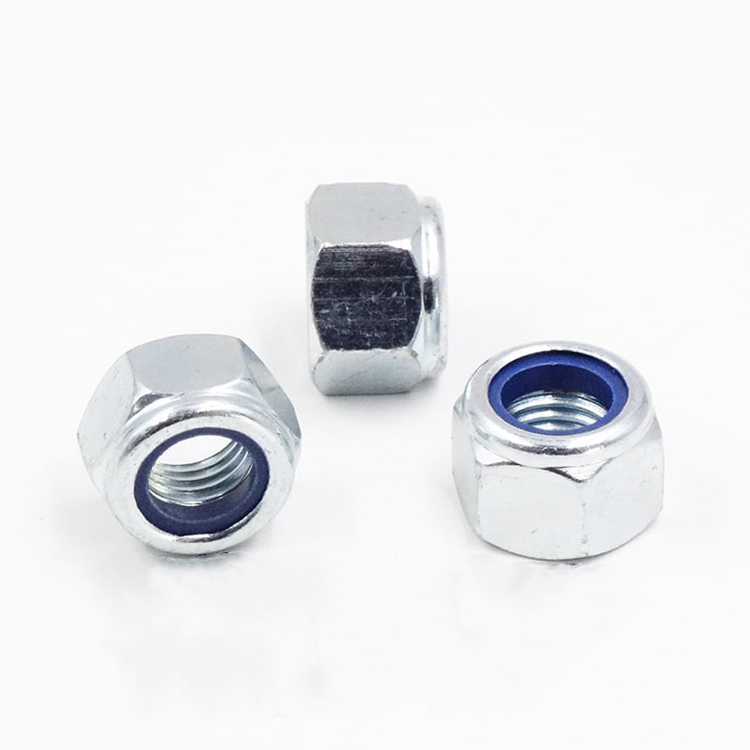
Centerpoint bolts are distinguished by their central positioning in mechanical structures, facilitating balanced force distribution. This is crucial in assemblies subjected to dynamic pressures, such as in automotive suspensions, aerospace components, and large-scale machinery. Proper alignment provided by these bolts minimizes wear and tear on associated components and reduces the likelihood of mechanical failures.
From the standpoint of expertise, one must understand that selecting the right centerpoint bolt involves considering several factors. The material composition is paramount; bolts are crafted from high-strength steel, titanium, or composite materials, depending on the application's specific stress and environmental conditions. For instance, in industries exposed to corrosive environments or extreme temperatures, selecting bolts made from corrosion-resistant alloys or those with specialized coatings can significantly enhance longevity and reliability.
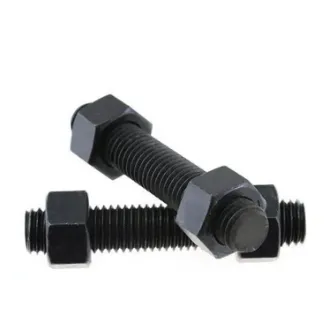
The thread pattern and pitch of centerpoint bolts also play a critical role in their effectiveness. Fine threads are generally used in precision applications requiring tight tolerances, while coarse threads are suitable for quick assembly and disassembly situations where speed and efficiency are prioritized. Furthermore, the length of engagement between the bolt and the substrate is critical to prevent shear or pull-out failures, particularly in high-load scenarios.
Authoritativeness in this domain is demonstrated by acknowledging industry standards and regulations. According to ISO and ANSI standards, centerpoint bolts must adhere to rigorous quality controls and testing to ensure they meet the requisite mechanical properties. Manufacturers often provide certification documents, which validate that their products comply with these established benchmarks, offering an added layer of trust and reliability.
centerpoint bolts
The trustworthiness of centerpoint bolts is further reinforced by the use of advanced manufacturing techniques. Precision manufacturing processes, such as CNC machining and thread rolling, ensure that bolts exhibit consistent geometrical properties and superior surface finishes. Quality assurance through non-destructive testing methods, like ultrasound or x-ray inspection, guarantees that each bolt is free of internal defects that could compromise its integrity in critical applications.
Customers and professionals seeking centerpoint bolts should also consider the supplier's reputation and track record. Vendors with a established history of reliability and customer satisfaction are more likely to deliver consistent quality and timely service. Investing in centerpoint bolts from reputable manufacturers not only ensures product performance but also aligns with the best practices in sourcing and procurement strategies.
Additionally, incorporating centerpoint bolts into a preventative maintenance program can extend the lifecycle of the entire assembly. Regular inspection, torque checking, and the replacement of worn bolts can prevent catastrophic failures and enhance operational efficiencies. This proactive approach, rooted in real-world experience, underscores the importance of treating centerpoint bolts as a critical investment rather than a mere component.
In conclusion, centerpoint bolts are a cornerstone of precision engineering, influencing the performance and safety of countless applications. Their strategic selection, underpinned by a deep understanding of material properties, threading dynamics, and adherence to industry standards, exemplifies the expertise and authority necessary in this field. By choosing high-quality centerpoint bolts and maintaining stringent quality assurance practices, industries can achieve greater reliability, efficiency, and trust in their mechanical systems.