Spring washers, often understated yet crucial, are vital components in various engineering applications. These seemingly humble devices, with their unique architecture and functionality, provide solutions to common mechanical problems such as loosening under vibration.
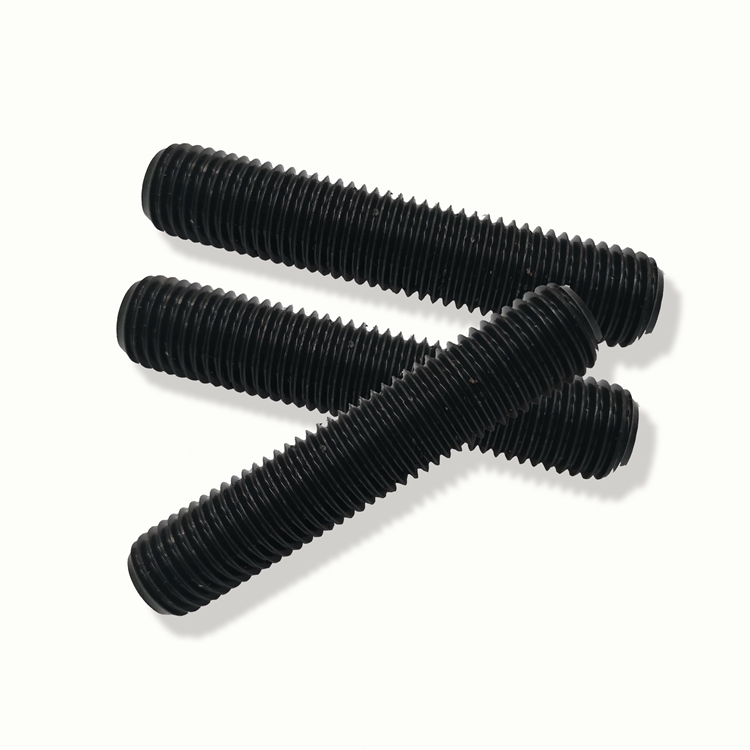
Distinct from other fastening tools, spring washers are specifically engineered to offer tension and absorb shock, thereby maintaining the tightness of bolts and nuts in dynamic conditions. Crafted from robust materials like stainless steel, phosphor bronze, and spring steel, these washers exhibit an impressive balance between elasticity and strength. Their resilience to deformation and exceptional tensile strength mark them as indispensable in applications where security and reliability are paramount.
From automotive industries to aerospace, these washers are a staple due to their ability to prevent joint failure. In an automobile engine, for instance, where consistent vibration can lead to the loosening of fasteners, spring washers provide the necessary tension to ensure that components remain securely fastened. Similarly, in the aerospace industry, maintaining the integrity of fasteners in fluctuating conditions is crucial. The application of spring washers ensures that aircraft components do not succumb to the stresses of flight.
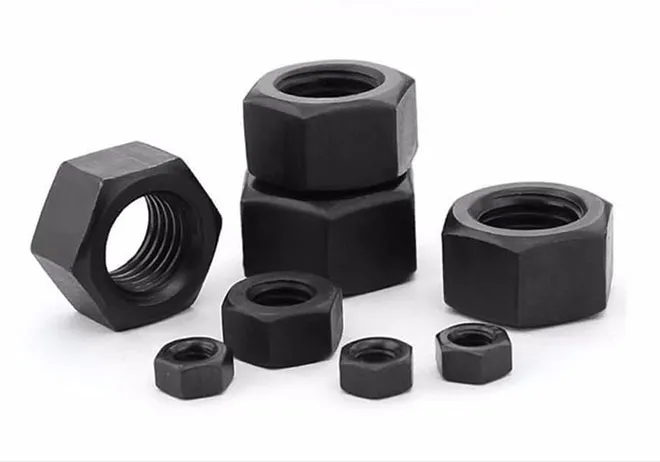
The versatility of spring washers expands their utility across different sectors. Their application in consumer electronics is testament to their ability to perform in precise and compact environments. With devices becoming increasingly sleek and lightweight, the need for components that assure durability without adding bulk is critical.
Spring washers meet this demand perfectly.
However, the true prowess of spring washers lies in their diversity. Available in various designs like Belleville washers, wave washers, and finger washers, each type caters to specific needs. The Belleville washer, for instance, known for its conical shape, offers high-load bearing capabilities while occupying minimal space. On the other hand, wave washers are employed for lightweight applications, providing consistent load deflection.
spring washer
Professionals leveraging these washers must consider the environment of application. Factors such as temperature, corrosive elements, and mechanical load play a significant role in the selection process. For example, selecting a stainless steel spring washer in environments prone to rust preserves the integrity of the fastener assembly.
Moreover, understanding the principle of load distribution is crucial when using spring washers. They not only offer resistance to loosening but also effectively distribute load over a surface, reducing the risk of damage to the material under the fastener. This characteristic is particularly beneficial in materials that are susceptible to compression or deformation.
The knowledge surrounding spring washer applications is profound, rooted in both empirical research and practical experience. Their effectiveness, backed by historical data and modern advancements, underscores their importance as a choice component in engineering practices. Assembling these washers requires precision, where the correct torque and alignment further accentuate their effectiveness in maintaining clamping force.
For experts and novices alike, selecting the correct type and understanding the mechanical principles behind spring washers can greatly enhance the longevity and safety of assemblies. The continuous evolution of materials and manufacturing techniques propels these components into newer, more dynamic applications, proving their adaptability to modern engineering challenges.
In conclusion, the role of spring washers transcends beyond a mere preventive tool. They are integral to the mechanics that ensure safety and functionality across industries. As an expert on this subject matter, promoting their correct application through an understanding of material science and mechanical dynamics enhances both performance and reliability in a multitude of environments.