In the realm of industrial applications, holding down bolts serve as vital components that ensure structural integrity and safety. These bolts, often overlooked, play a key role in securing machinery, pillars, and other heavy structures, helping prevent catastrophic failures.
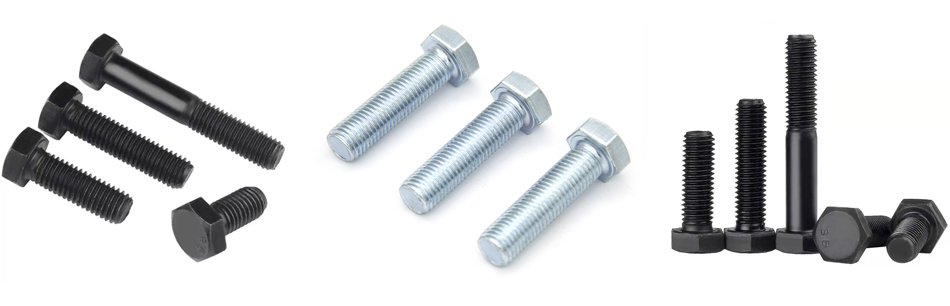
Drawing from extensive experience in the field of structural engineering, it becomes evident that choosing the right type of holding down bolt is as crucial as their installation. These bolts come in various forms, such as L-shaped, J-shaped, and straight, each designed to meet specific structural needs. The choice largely depends on the nature of the foundation and the type of load it needs to bear. For instance, L-shaped bolts are ideal for insubstantial loads, providing reliable service by anchoring securely into concrete. J-shaped bolts, offering a more adaptable design, serve better where adjustments might be necessary post-installation.
The expertise involved in utilizing these bolts goes beyond their selection. An optimal installation demands precision and understanding of the structure's requirements. Holding down bolts must be embedded in concrete at precise angles to align with the structural framework. This precise alignment ensures even load distribution across the bolt, preventing undue stress on a singular point that could lead to fracture or failure.
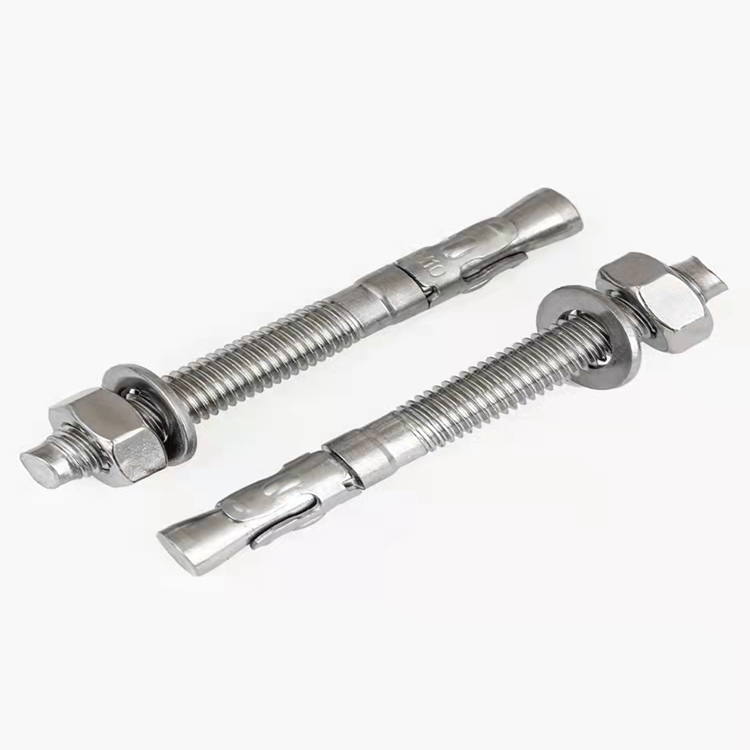
Professionals often emphasize the importance of embedding depth. The embedment must be sufficiently deep to counteract tension forces that might otherwise threaten to pull the bolt from its foundation. Calculations concerning embedment depths are performed using standardized guidelines that consider factors such as bolt length, diameter, and the characteristics of the concrete used.
holding down bolts
Furthermore, industry authorities recommend corrosion prevention measures to maintain the reliability of holding down bolts over time. Exposure to the elements can compromise the integrity of these fasteners. Therefore, materials such as stainless steel or hot-dip galvanized finishes are chosen for their resistance to rust and corrosion. High-quality coatings can significantly extend the life of the installation, maintaining both the structural integrity and the aesthetic appeal of the construction.
The trustworthiness of holding down bolts is not just a factor of their composition or installation; it also lies in regular maintenance and inspections. Experienced structural engineers suggest periodic reviews and tests, especially in situations where the load dynamics might change or in environments with high exposure to corrosive elements. Non-destructive testing methods, such as ultrasonic or radiographic methods, enable comprehensive inspections without dismantling the entire setup, ensuring ongoing safety and functionality.
In summation, holding down bolts are indispensable in ensuring the safety and reliability of numerous structures. The combination of selecting the appropriate type of bolt, exacting installation procedures, corrosion prevention measures, and regular maintenance underscores their effectiveness and longevity. The systemic use of these practices forms the cornerstone of any robust structural project that relies on holding down bolts. Moreover, by fostering a culture of meticulous planning and maintenance, engineers can assure stakeholders of the structure’s resilience, thus enhancing trust and confidence in the project’s long-term viability.