Stud bolts are critical components in numerous industrial applications, providing the essential link in structures where fastening strength, reliability, and durability are paramount. They are predominantly used in industries such as oil & gas, petrochemical, and power generation, where the robustness of fastening systems directly impacts operational safety and efficiency. Understanding the nuances of stud bolt screws can dramatically affect the quality and performance of any project.
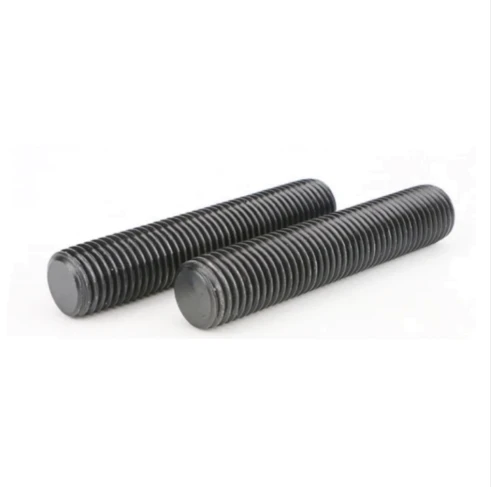
A stud bolt, essentially a threaded rod with nuts at both ends, is designed to withstand high levels of tension and stress. Expertly manufactured from materials like stainless steel, alloy steel, or high-grade carbon steel, they boast exceptional strength and rust resistance. In environments where heavy machinery and equipment are commonplace, these bolts must meet stringent regulatory standards, underscoring their importance in maintaining structural integrity and safety.
Experience in utilizing stud bolts reveals several key factors influencing their effectiveness. Installation precision is paramount. Incorrect torque during installation can lead to either over-tightening or inadequate tension, both of which can compromise joint integrity, leading to equipment failure or catastrophic accidents. It is advisable to use calibrated torque wrenches to ensure that each bolt is secure to its intended specifications. Moreover, using a lubricant such as molybdenum disulfide can significantly reduce friction during tightening and ensure even distribution of force.
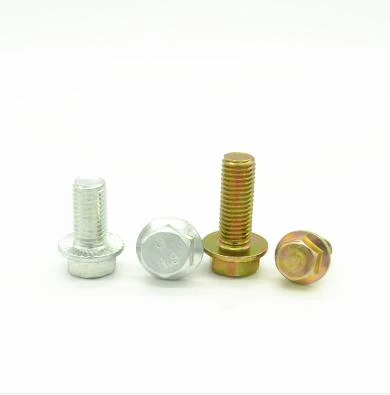
Expertise in the discipline highlights the importance of choosing the right type of stud bolt for specific applications. Each type of bolt — whether B7, L7, or B16 — possesses unique properties tailored for particular environments. For instance, B7 stud bolts, made from chromium-molybdenum steel, offer excellent heat resistance, making them ideal for high-temperature applications. Conversely, B16 bolts are suitable for environments involving pressures where both temperature and corrosion resistance are vital. Selecting the wrong material or size can lead to increased wear and frequent maintenance, ultimately impacting operational costs.
stud bolt screw
The authoritative nature of stud bolts is underscored by the stringent standards set by industries and international organizations. Standards such as ASTM A193 and A320 provide comprehensive guidelines concerning dimensions, materials, and mechanical properties. Compliance ensures that the bolts can adequately support the intended loads over extended periods. It is crucial to work with manufacturers and suppliers who have a proven track record of delivering products that meet these standards, as this collaboration guarantees that the bolts perform optimally within their designated contexts.
Trustworthiness plays a significant role in both the selection and application of stud bolts. Partnering with suppliers who offer verifiable product certifications, traceability, and accountability ensures that the bolts you use uphold quality and compliance with essential safety standards. Furthermore, consistent training and familiarization with new technologies and techniques in bolt application enhance workforce competence, reducing the risk of installation errors and improving overall system reliability.
In addition, leveraging advancements in technology, such as Computer-Aided Design (CAD) in the customization of stud bolts, provides a tailored fit for specific applications, elevating performance while reducing waste. These technological integrations signify a modern approach to tackling old challenges faced in heavy industries.
In summary, the strategic application of stud bolts is the linchpin in achieving robust and safe structural connections in complex environments. The intricate blend of experience, technical proficiency, authoritative guidelines, and trustworthy processes ensures that stud bolts not only fulfill but exceed the demands of modern engineering challenges. As industries continue to evolve, staying informed about best practices and innovations in stud bolt technology will remain essential for maintaining efficiency, safety, and reliability in all applications.