Stud bolts are a fundamental component in many industrial settings, offering significant advantages in terms of reliability and versatile application. These fasteners, which are essentially rods with threads on both ends, are primarily utilized for flange connections in industries ranging from oil & gas to chemical processing and power generation.
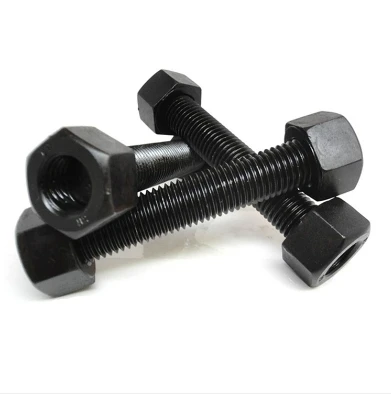
Their primary function is to achieve a secure and removable connection between pipes, valves,
and other equipment. The effectiveness of a stud bolt is heavily dependent on the material selection, installation procedures, and maintenance practices, all of which underscore the experience and expertise required to work with them effectively.
From a material perspective, stud bolts are manufactured from a variety of metals, including carbon steel, stainless steel, and exotic alloys such as Inconel and Monel. This diversity allows them to withstand extreme temperatures, high pressures, and corrosive environments. For instance, in a petrochemical plant, where exposure to harsh chemicals is commonplace, opting for a material like stainless steel ensures longevity and reduces the risk of failure. Such choices require a deep understanding of material science and industry-specific demands, underpinning the expertise that professionals bring into play.
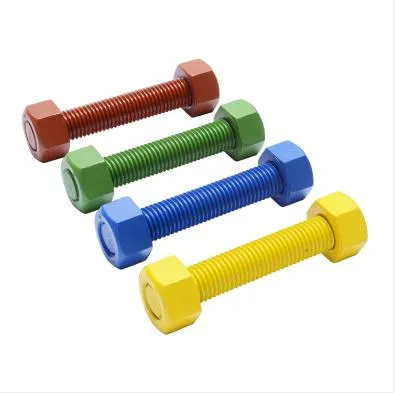
The correct installation of stud bolts is equally paramount. Proper torque application ensures optimal tension, preventing leaks and maintaining the integrity of the joint. This precision in installation highlights the need for comprehensive training and experience. Technicians must be aware of various factors, including the temperature of the operating environment and the potential for thermal expansion, which can affect the tightening process. Deploying techniques like torque wrenches or even more advanced hydraulic torque tools helps achieve the right tension, underscoring the critical nature of expertise and experience in stud bolt installation.
stud bolt
Authoritativeness in the use of stud bolts is derived from adhering to international standards such as those from the American Society of Mechanical Engineers (ASME) or the American Petroleum Institute (API). Following these standards ensures that the application not only meets legal and safety requirements but also reinforces the credibility of the engineering processes involved. Companies that adhere strictly to these standards are often more trusted and regarded as leaders in their field, adding a layer of trustworthiness to their operations.
To ensure trustworthiness in the performance of stud bolts, regular inspection and maintenance are crucial. Non-destructive testing methods such as ultrasonic testing or magnetic particle inspection can be employed to detect any defects or corrosion that might compromise their integrity. Maintenance schedules should be strictly followed, with records meticulously kept, providing a transparent view of the fastener’s lifecycle and ensuring safety and reliability.
In conclusion, the effective use of stud bolts hinges on a combination of material suitability, precise installation, adherence to authoritative standards, and diligent maintenance. This multifaceted approach not only enhances performance but also fosters a culture of safety and reliability. By leveraging deep industry expertise and maintaining rigorous standards, professionals ensure that stud bolts remain a critical component in the safe and efficient operation of vital industries. Through these practices, companies affirm their commitment to quality, sustainability, and operational excellence, reflecting a deep-seated trustworthiness that resonates with their commitment to excellence in engineering and safety.