Rust-proof bolts play a pivotal role in industries where durability and reliability are crucial. These bolts are specifically designed to withstand the harshest environments, ensuring the integrity of structures and machinery over extended periods. In sectors like construction, maritime, and automotive, the demand for rust-proof fastening solutions has been steadily growing due to their enhanced longevity and low maintenance needs.
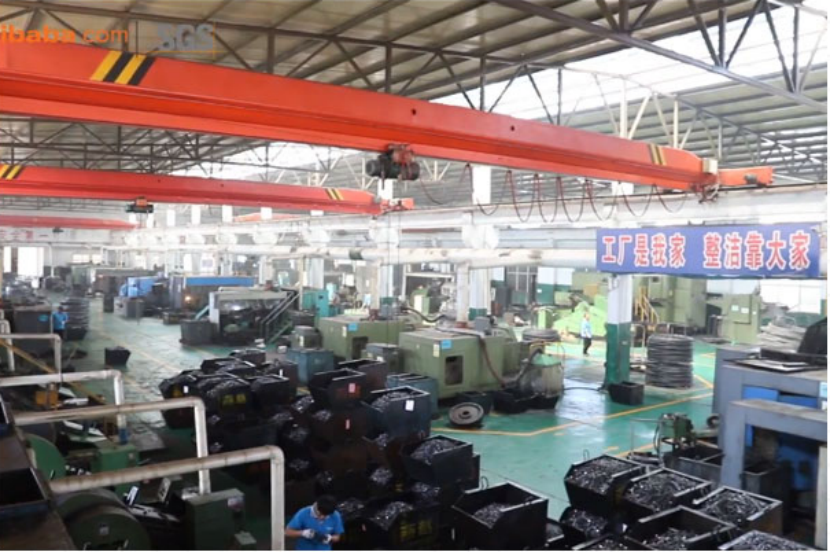
The secret behind rust-proof bolts lies in the materials and coatings used. Typically, these bolts are made from stainless steel or are coated with substances like zinc or hot-dip galvanization. Stainless steel bolts are known for their corrosion resistance and high tensile strength, making them suitable for a wide range of applications. In contrast, zinc-coated bolts provide cost-effective protection, creating a barrier against moisture and corrosive elements.
Professionals who have worked extensively with rust-proof bolts often emphasize their reliability in adverse conditions. For instance, in coastal construction projects where saltwater exposure is inevitable, using rust-proof bolts prevents structural compromises, which could lead to catastrophic failures. Engineers and contractors consistently prioritize these bolts to avoid costly repairs and replacements over time.
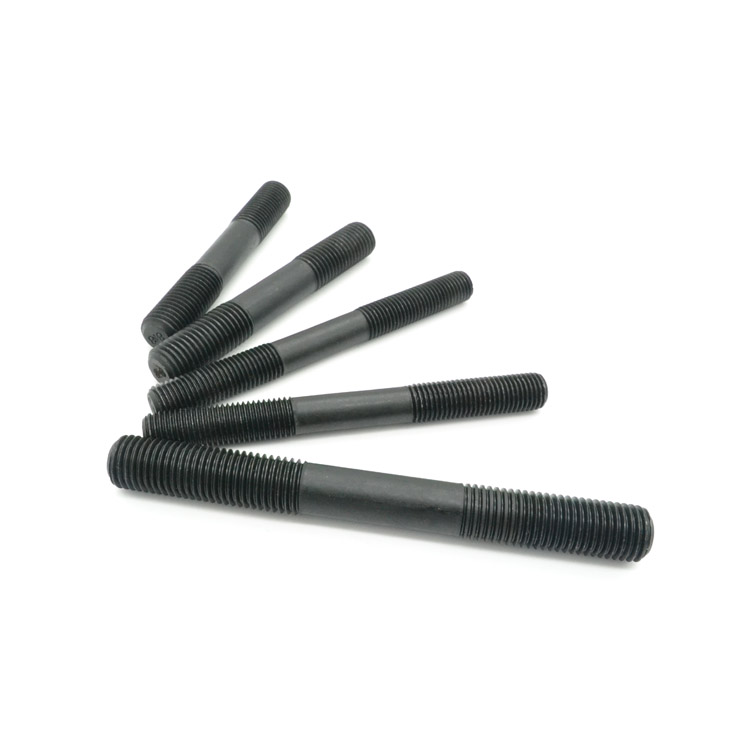
Furthermore, expertise in selecting the right type of rust-proof bolt can significantly impact project outcomes. Knowing when to use stainless steel bolts versus when to opt for zinc-coated variants requires an understanding of the specific environmental pressures that the bolts will face. For example, automotive experts often choose different coatings depending on whether the vehicles are intended for arid regions or areas with heavy snowfall.
Authoritativeness in this domain is backed by decades of research and development. Manufacturers invest in cutting-edge technology to produce bolts that meet rigorous industry standards. Many of these companies are ISO certified, which ensures that their products consistently maintain quality and safety benchmarks. These certifications further establish trust with clients, who rely on these components for building dependable infrastructure.
rust proof bolts
Trustworthiness is inherently linked to the performance of rust-proof bolts over time. Real-life case studies showcase scenarios where high-quality bolts have prolonged the lifespan of bridges, buildings, and machinery under constant stress. Feedback from industry veterans and ongoing testimonials from satisfied customers provide additional layers of credibility to the proven track record of these bolts.
An essential aspect of rust-proof bolts is their contribution to sustainability. By reducing the frequency of replacements and minimizing material wastage, these bolts contribute to eco-friendly practices. Moreover, the reduced need for chemical treatments to combat rust aligns with environmentally conscious construction and manufacturing protocols.
For those looking to purchase rust-proof bolts, understanding the specifics of their applications can dictate the best choice. Whether it’s a marine engineer ensuring that offshore platforms remain stable, or an automotive designer tasked with producing durable vehicles, choosing the right bolt can be a crucial decision. Optimization of rust-proof bolt use not only enhances structural integrity but also instills confidence in the longevity of the entire system.
In conclusion, rust-proof bolts are more than just essential components; they are fundamental to the success and safety of modern engineering marvels. Leveraging their advantages requires a blend of experience, expertise, authority, and trust. As industries evolve, the permanence promised by rust-proof technology remains a critical asset in creating sustainable and resilient structures.