Understanding Flat Socket Head Cap Screws A Comprehensive Guide on Manufacturing
Flat socket head cap screws, often abbreviated as FHCS or simply socket head caps, are a type of fastener that play a crucial role in various engineering and manufacturing applications. These screws are characterized by their low profile, flat heads, and a hexagonal socket for tightening with a wrench or driver. In this article, we delve into the intricacies of their manufacturing process, the materials used, and their importance in modern industries.
Manufacturing Process
The production of flat socket head cap screws involves a series of precise steps. It typically begins with the selection of raw materials. High-quality steel, stainless steel, titanium, aluminum, or other alloys are commonly used, depending on the specific requirements of strength, durability, and resistance to corrosion.
The first stage is forging, where the chosen metal is heated to high temperatures and then shaped into rough screw blanks using a die. This process imparts the initial shape and strength to the screw. Following forging, the blanks are then headed, which involves forming the head of the screw using a press.
Thread rolling is the next critical step. Unlike cutting threads, which removes material, rolling threads deforms the blank's surface to create the thread pattern. This results in stronger threads with better fatigue resistance. The screws are then heat-treated to enhance their mechanical properties, such as hardness and tensile strength.
After heat treatment, the screws undergo a surface finish process
After heat treatment, the screws undergo a surface finish process
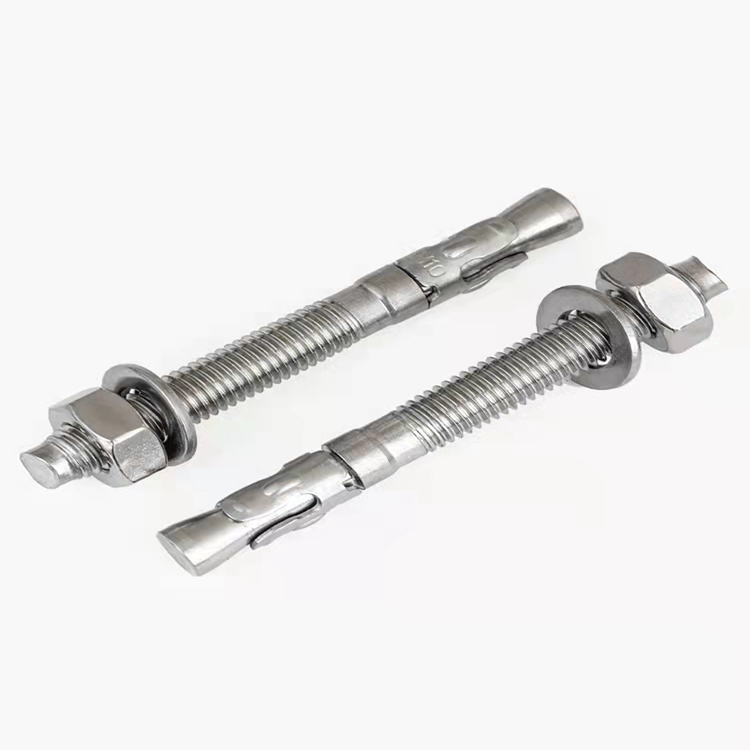
After heat treatment, the screws undergo a surface finish process
After heat treatment, the screws undergo a surface finish process
flat socket head cap screws manufacturer. This could be anything from a simple cleaning to more complex treatments like plating or anodizing, which not only enhances their appearance but also improves corrosion resistance. Finally, the screws are quality-checked for dimensional accuracy and surface finish before being packaged and shipped to manufacturers worldwide.
Applications and Importance
Flat socket head cap screws find extensive use in industries ranging from automotive and aerospace to electronics and construction. Their compact design allows them to fit into tight spaces, while the socket head enables a more secure grip and prevents damage to surrounding surfaces. The flat head ensures a flush fit, making them ideal for applications where a clean, streamlined look is desired.
In aerospace, for instance, these screws are used in aircraft assemblies due to their strength and resistance to high stress. In electronics, they are used for their small size and ability to provide a secure hold without protruding above the surface. The manufacturing industry relies on these screws for their precision and durability in machinery assembly.
Conclusion
Flat socket head cap screws, though seemingly small, play a significant role in numerous industrial applications. The manufacturing process, from selecting the right material to the final quality check, is a testament to the importance placed on precision and performance. As technology advances, the demand for these specialized screws is likely to grow, making their manufacturing a vital part of the global manufacturing landscape. Understanding their manufacture and function can help engineers and designers make informed decisions when specifying fasteners for their projects.