The Significance of OEM 10 32 Screws in Modern Manufacturing
In the world of manufacturing and engineering, every component, no matter how small, plays a crucial role in the overall functionality and integrity of a product. This is particularly true for the seemingly insignificant yet indispensable part known as the OEM 10 32 screws. These screws, though they may seem like a mere speck in the grand scheme of things, are integral elements that hold together a wide array of devices, machinery, and structures.
OEM stands for Original Equipment Manufacturer, indicating that these screws are specifically designed and produced by the original manufacturer to fit their equipment or devices perfectly. The in the term is simply a URL encoding for the space character, used to ensure compatibility in digital platforms. The 10 and 32 denote the screw's size - the former referring to the diameter in inches, and the latter to the thread pitch, which is the distance between each thread.
The significance of the OEM 10 32 screws lies in their precision and compatibility. Unlike generic screws, these are tailored to meet the exact specifications of the equipment they are intended for, ensuring a secure and efficient fit. Their precise threading and dimensions minimize the risk of stripped threads, loose connections, or damage to the device, thereby enhancing the reliability and longevity of the equipment.
Moreover, these screws often undergo rigorous quality control measures, ensuring they meet stringent standards for strength, durability, and resistance to environmental factors such as corrosion
Moreover, these screws often undergo rigorous quality control measures, ensuring they meet stringent standards for strength, durability, and resistance to environmental factors such as corrosion
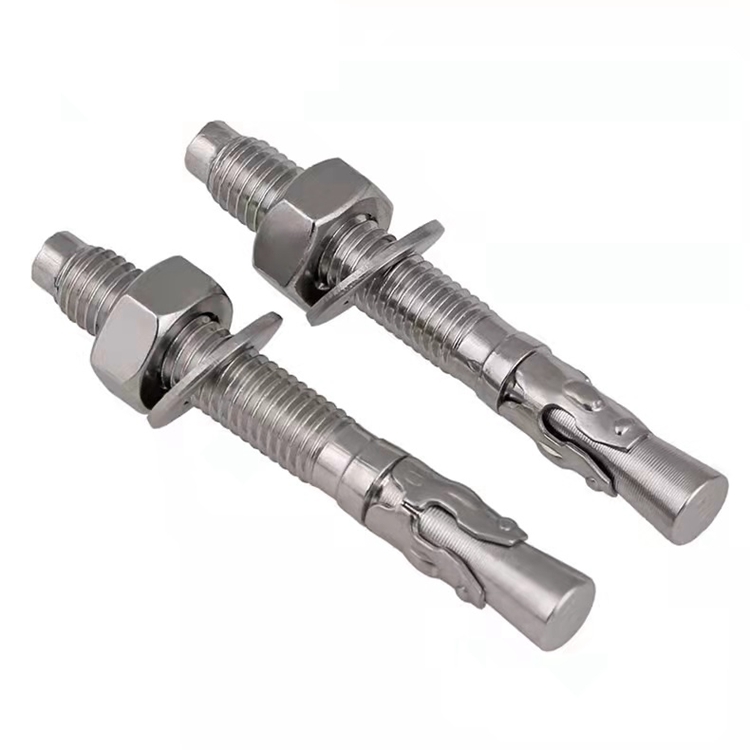
Moreover, these screws often undergo rigorous quality control measures, ensuring they meet stringent standards for strength, durability, and resistance to environmental factors such as corrosion
Moreover, these screws often undergo rigorous quality control measures, ensuring they meet stringent standards for strength, durability, and resistance to environmental factors such as corrosion
oem 10 32 screws. Their usage can significantly reduce maintenance costs and downtime, as they are less prone to failure compared to their non-OEM counterparts.
In industries like automotive, aerospace, electronics, and construction, where precision and safety are paramount, the use of OEM 10 32 screws is non-negotiable. They are instrumental in securing critical components, from engine parts in cars to microchips in electronic devices, and even structural elements in buildings.
However, it's not just about the physical function. The choice of using OEM 10 32 screws also reflects a commitment to maintaining the integrity of the original design, honoring the manufacturer's vision, and upholding the warranty and performance expectations of the end-users.
In conclusion, while the humble OEM 10 32 screws might not be the most glamorous aspect of modern manufacturing, they undeniably form the backbone of countless products and systems. Their importance cannot be overstated, as they embody the principle of 'small but mighty', quietly holding together the complex machinery of our modern world. It's a testament to the power of thoughtful design and the significance of even the tiniest details in creating reliable, high-performance products.