The Art and Science of Carbon Steel Hex Bolts Manufacturing
In the world of fasteners, carbon steel hex bolts stand out as both a symbol of industrial strength and an embodiment of precision engineering. These ubiquitous components are not merely simple pieces of metal; they are the result of a carefully crafted manufacturing process that ensures their reliability and durability in various applications.
Manufacturers of carbon steel hex bolts follow stringent procedures to meet the high demands of the construction, automotive, and aerospace industries. The journey from raw material to finished product is a testament to the blend of art and science that goes into making these essential fasteners.
The production begins with selecting high-quality carbon steel, a versatile alloy known for its excellent strength and resilience. This choice of material is crucial, as it determines the final properties of the bolt, such as its ability to withstand stress and resist corrosion.
Once the steel is chosen, it enters the manufacturing phase. The steel is heated to malleable temperatures and then rolled or forged into wire rods. These rods are subsequently drawn through dies to achieve the desired diameter, which is a critical step in ensuring consistency across the production line.
Next, the heads of the bolts are formed, either by cold heading or hot forging. Cold heading involves compressing the material at room temperature, while hot forging heats the steel to form the head shape. Both methods require precise control to ensure the integrity of the bolt's structure Both methods require precise control to ensure the integrity of the bolt's structure
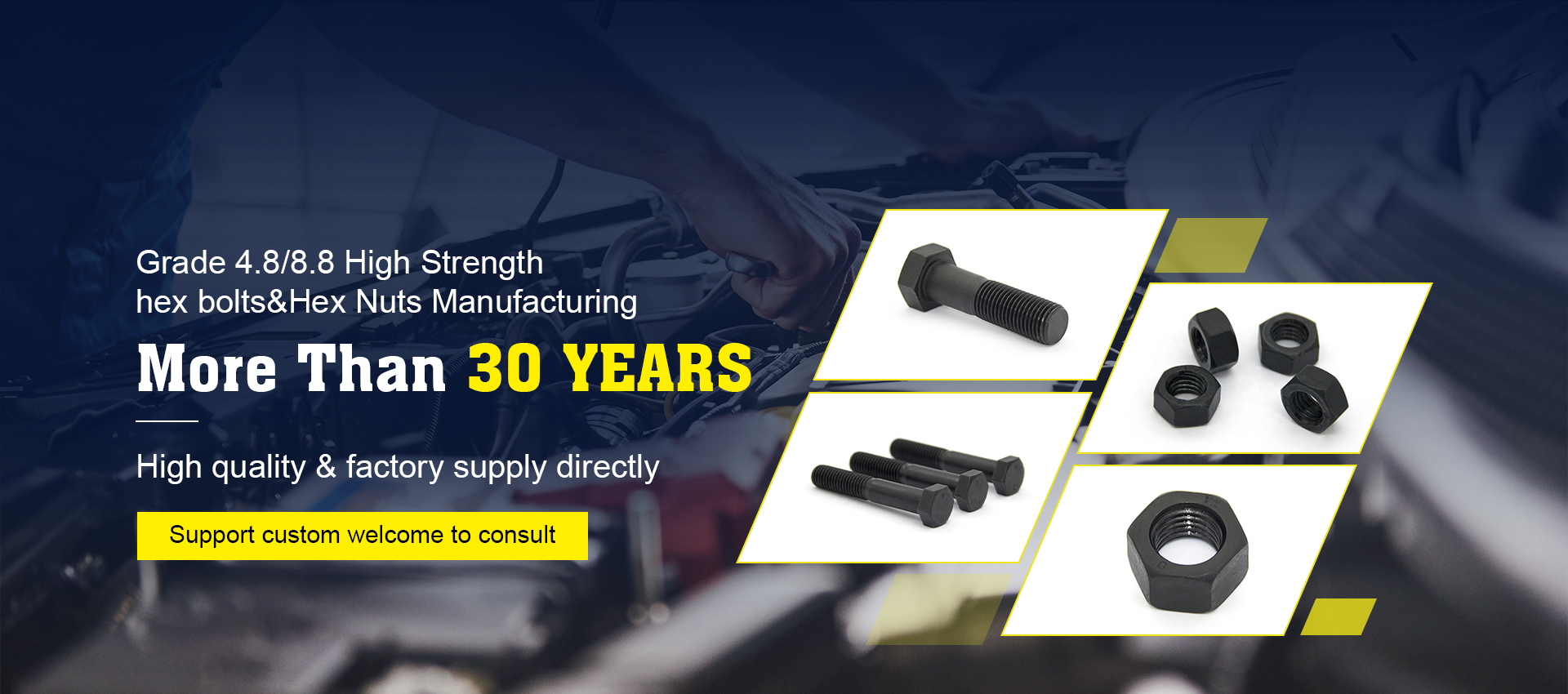
Both methods require precise control to ensure the integrity of the bolt's structure Both methods require precise control to ensure the integrity of the bolt's structure
carbon steel hex bolts manufacturer.
Following this, the threads are cut into the shaft of the bolt, a meticulous process that requires exacting tolerances. Each thread must be consistent and clean to guarantee a firm grip when the bolt is mated with a nut.
Quality control is paramount throughout the manufacturing process. From the initial stages of material selection to the final inspection, manufacturers employ rigorous testing to certify that every bolt meets industry standards. This may include tests for tensile strength, hardness, and torque resistance.
Finally, the bolts are often coated to enhance their corrosion resistance and provide a smooth finish that facilitates installation. Zinc plating, for instance, offers a barrier against environmental factors that could compromise the bolt's structural integrity.
Carbon steel hex bolt manufacturers are not just producers of hardware; they are custodians of an intricate process that marries metallurgy with precision engineering. By adhering to strict protocols and embracing innovation, these manufacturers continue to supply industries with reliable fasteners that are the unsung heroes of countless structures and machines worldwide.