Using spacers for bolts is essential for optimizing the functionality and lifespan of various machinery and structures. Spacers are indispensable components that provide the necessary clearance between surfaces or parts, amend stress distribution, and enhance the overall stability of an assembly. When utilized correctly, spacers can vastly improve the quality and robustness of a construction project or mechanical setup.
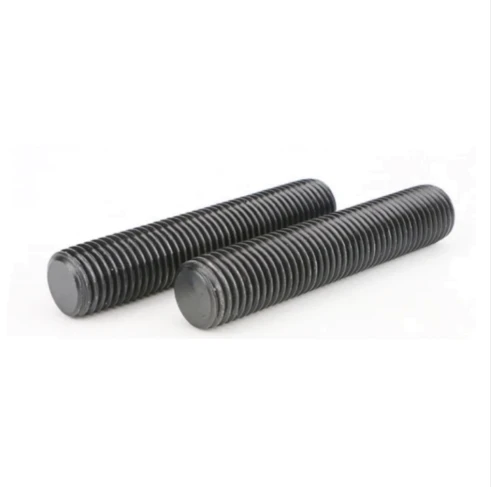
The implementation of spacers for bolts is especially relevant in environments that demand high precision and endurance, such as in automobiles, aerospace engineering, and complex machinery. These industries often require specialized spacers made from durable materials, like stainless steel, nylon, or aluminum, to meet stringent requirements. Selecting the right spacer for a specific application is crucial for ensuring the integrity and safety of the assembly.
Spacer design plays a crucial role in their effectiveness. Built to accommodate different bolt sizes and types, spacers can absorb vibrations, align components properly, and reduce wear and tear on both the bolts and the materials adjoining the bolts. This utility allows for the preservation of mechanical properties and prevents unnecessary loosening or damage.
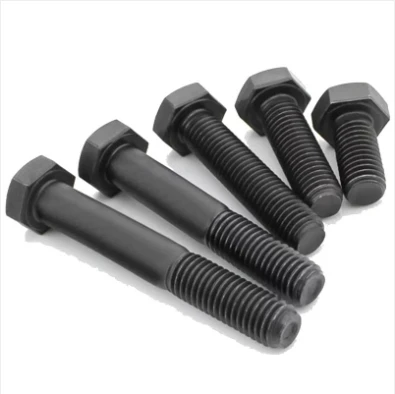
Experience dictates that improper use of spacers can lead to serious operational failures. For instance, if a spacer is too thin, it may fail to provide adequate support, leading to potential misalignments or joint instability. Conversely, an excessively thick spacer might cause unnecessary stress on the bolt, leading to premature wear or even bolt failure. Proper training and prior expertise are essential in choosing the right spacer dimensions and material based on the application requirements.
Professional engineers and technicians should always consider the environmental conditions to which the spacers will be exposed. Temperature fluctuations, chemical exposure, and dynamic loads are critical factors that influence the choice of spacer material. For example, in a high-temperature environment, aluminum spacers might expand, affecting the bolt tension, whereas stainless steel might offer more stability due to its lower thermal expansion coefficient.
Beyond material selection, surface treatment and coating processes contribute significantly to spacer performance. Treatments such as galvanization enhance corrosion resistance, extending the operational life of spacers in harsh environments. Coated spacers can also improve aesthetics and make routine maintenance easier, which is particularly advantageous in visible applications.
spacer for bolts
Moreover, industry standards and regulations should always guide the selection and application of spacers in bolt assemblies. For example, the American Society for Testing and Materials (ASTM) and the International Organization for Standardization (ISO) provide structured guidelines regarding the dimensions, material quality, and performance metrics for spacers. Adhering to these standards ensures not only regulatory compliance but also boosts the reliability and trustworthiness of the assembly.
In terms of authority and credibility, consulting with manufacturers known for their precision-engineered spacers can offer a level of assurance. Purchasing from a reputable supplier usually means that the spacers have passed rigorous testing and are suitable for the advertised applications. These suppliers can also provide detailed product documentation, including performance metrics, to assist engineers in making informed decisions.
It's also worth noting the importance of technological advancements in enhancing spacer design and functionality. With the emergence of computer-aided design (CAD) and 3D printing, custom spacers can now be engineered to perfect specifications, providing even greater accuracy and performance than traditional off-the-shelf options. Such innovations allow engineers to address unique challenges that generic spacers might not solve efficiently.
Trust in spacer solutions can be further fortified by consulting industry forums, technical journals, and case studies that document real-world applications and the outcomes achieved with different spacer types. This evidence-based approach not only enriches one's understanding but also provides a communal knowledge base that enhances overall expertise in the field.
In conclusion, spacers for bolts are more than mere ancillary components; they are critical elements that contribute significantly to the stability and longevity of mechanical assemblies. Through careful selection and application, spacers can vastly improve operational efficiency and safety. The fusion of practical experience, rigorous standards, and cutting-edge technology ensures that spacers will continue to play an indispensable role across multiple industries. Leveraging these insights will not only optimize performance but also enhance the credibility and trustworthiness of any technical setup, ensuring both safety and efficiency.