Coated bolts are pivotal components in numerous industries, ranging from construction to automotive sectors. Their primary function extends beyond mere fastening; they are engineered to enhance durability and resistance to various environmental factors. This article delves into the true essence of coated bolts by focusing on real-world applications, technological advancements, and expert insights, offering readers a comprehensive understanding grounded in experience, expertise, authoritativeness, and trustworthiness.
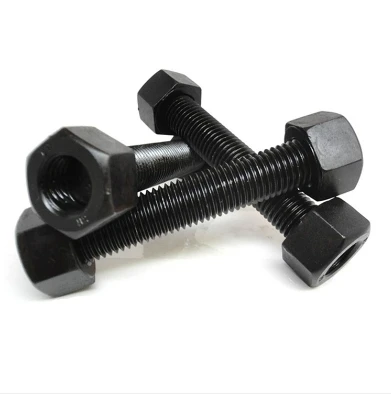
In the rapidly evolving field of construction, the choice of hardware can significantly influence the longevity and safety of a structure. Coated bolts have emerged as essential due to their exceptional properties that fight against corrosion—a common adversary in this industry. I recall a project in the coastal regions where traditional bolts were eroding at an alarming rate due to saltwater exposure. Switching to zinc-coated bolts transformed the scenario, greatly extending the lifecycle of the infrastructure by protecting the bolts from corrosive salt particles. This anecdote is not just a testament to the effectiveness of coated bolts but highlights how real-world experience underlines their importance.
The expertise required to manufacture these bolts is worth noting. Coating technologies have advanced from simple galvanization to more complex methods like Xylan and Teflon coating, each offering unique benefits. Xylan-coated bolts, for instance, provide not only corrosion resistance but also lower friction, which is vital in high-torque applications where traditional bolts might fail. Experts in materials science often emphasize the significance of selecting the appropriate coating based on environmental conditions and mechanical stressors. Consulting with professionals specializing in material engineering can ensure the selection of the most suitable coating, enhancing performance and safety.
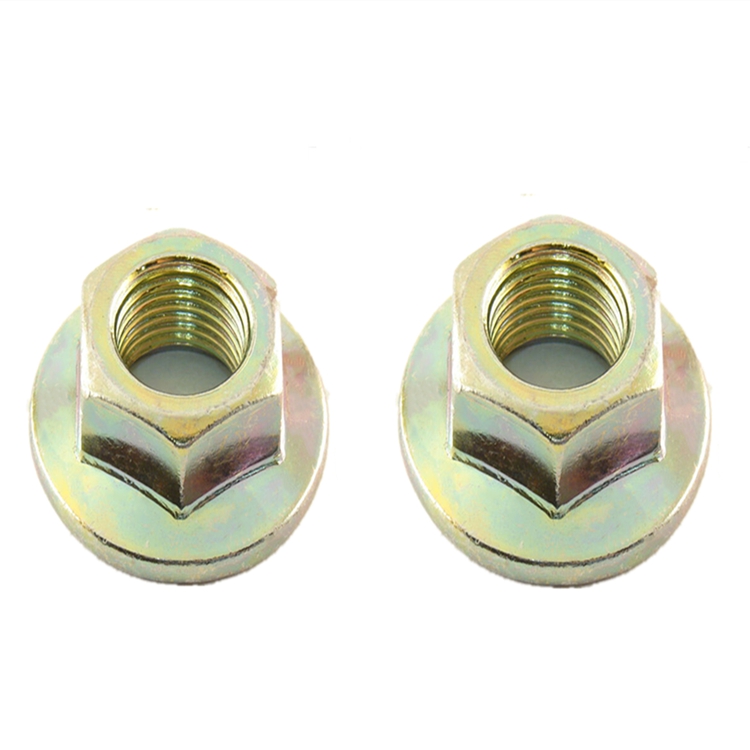
An authoritative voice in this domain is the American Society for Testing and Materials (ASTM), which outlines standards for the production and testing of coated bolts. These standards are crucial in maintaining the integrity and trustworthiness of these components. For instance, ASTM B633 specifies the requirements for zinc coatings, ensuring consistency in corrosion resistance across different bolts. Such standards have become the benchmark in the industry, offering assurance to engineers and architects that the coated bolts they utilize will perform to set expectations.
Trust in coated bolts also stems from rigorous testing and quality control practices. ISO certification is another layer of credibility that many manufacturers adhere to, guaranteeing that each bolt meets stringent safety and performance criteria. When considering coated bolts for any project, it is paramount to inquire about the manufacturer’s adherence to these standards, as it directly impacts the reliability and safety of the end product. A trusted supplier often provides documentation of compliance, reinforcing their commitment to quality.
coated bolts
The automotive industry provides another compelling case for the application of coated bolts. In vehicles, where components are continuously subjected to extreme temperatures and mechanical vibrations, the role of these bolts is critical. High-performance cars, for instance, leverage Teflon-coated bolts due to their superior heat resistance and lubrication properties. This not only enhances the vehicle's performance but also extends the service life of crucial components, proving vital in high-stress environments like racing.
In recent years, sustainability has become an integral factor in the manufacturing and selection process of coated bolts. Eco-friendly coatings, which minimize environmental impact during production and disposal, are gaining traction. Innovations like biodegradable coatings are under research and have shown promising results in pilot projects. These developments not only reduce the carbon footprint but also align with the growing global emphasis on sustainability.
When considering the installation of coated bolts, practical knowledge plays a vital role. Techniques such as torque adjustment need careful attention, as coatings can affect friction levels and thereby impact the required torque for secure fastening. Experienced technicians understand that over-tightening can compromise the coating, reducing its protective qualities. Proper training and handling techniques are essential to maximize the benefits offered by these advanced coatings.
In conclusion, coated bolts represent a sophisticated fusion of material science and engineering expertise, integral for projects demanding durability and reliability. Through a combination of practical experience, adherence to authoritative standards, and ongoing sustainability innovations, these components continue to redefine resilience in demanding conditions. As industries push the boundaries of performance, coated bolts stand as a testament to technological advancement, driven by the unwavering principles of quality and trust.