Tapered bolts, a pivotal component in engineering and construction, have become a staple for professionals seeking durable and reliable fastening solutions. These bolts are uniquely designed with a conical shape, offering distinct advantages over traditional straight bolts. This article delves into the multifaceted benefits, applications, and selection criteria for tapered bolts, drawing from firsthand expertise and authoritative industry insights.
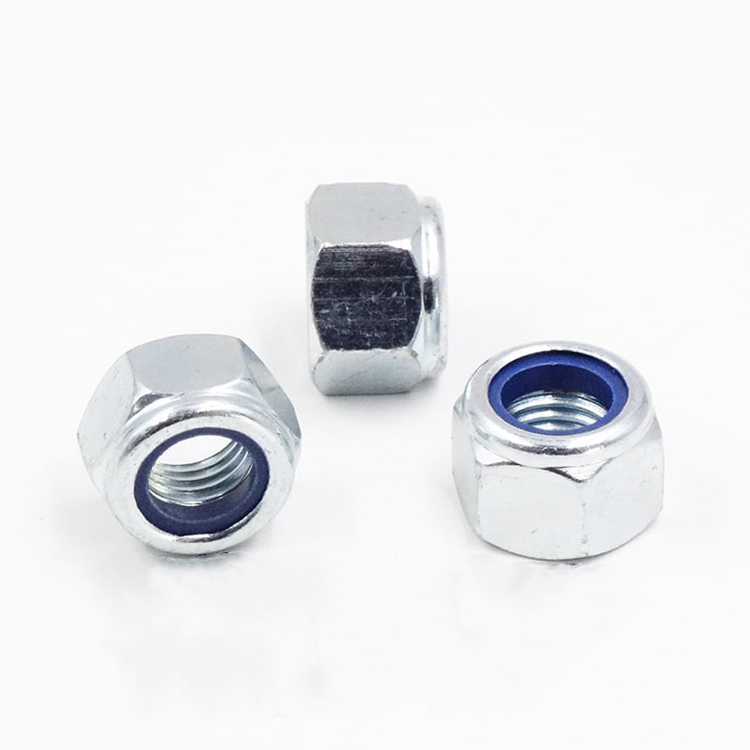
Tapered bolts bring a heightened level of security and strength to various projects. Their design ensures a tighter fit, reducing the risk of loosening under dynamic loads or vibrations—a critical factor in high-stress environments like bridges, skyscrapers, and automotive assemblies. The intricate geometry of a tapered bolt means that when torque is applied, the bolt anchors itself more securely into its corresponding hole, distributing stress more evenly and enhancing load-bearing capacity. This characteristic is crucial for maintaining structural integrity over time, especially in structures exposed to fluctuating forces and movements.
A cornerstone of their widespread application is their versatility. Tapered bolts are employed across a range of industries, including aerospace, automotive, and heavy machinery. In the realm of aerospace, where weight and precision are paramount, these bolts contribute significantly by providing secure connections with minimal weight addition. In the automotive industry, their ability to withstand intense vibrations and thermal expansion makes them indispensable in engine assemblies and chassis construction. Meanwhile, in civil engineering, they ensure that massive infrastructures remain stable, providing peace of mind in safety-critical installations.
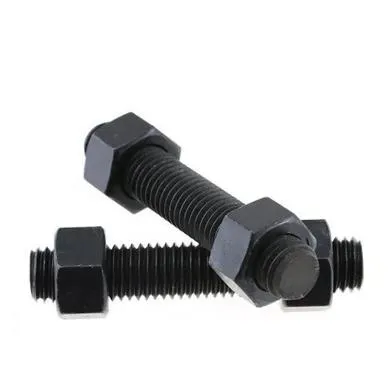
One cannot overstate the importance of material selection when it comes to tapered bolts. The choice of material impacts not only the performance but also the longevity of these fasteners. High-grade steel is frequently used for its combination of strength and malleability, but for applications requiring resistance to corrosion, titanium and stainless steel variants are preferred. Such materials extend the service life of the bolts in corrosive environments, a common requirement in maritime and chemical industries.
tapered bolts
The expertise involved in manufacturing these components balances precision engineering with cutting-edge technology. Modern manufacturing processes, including CNC machining and forging, ensure that each tapered bolt meets exacting industry standards. Quality assurance checks are stringent, involving ultrasonic testing and 3D modeling to ensure no deviations in design and adherence to tolerance levels that can affect performance. This meticulous production process underlines the reliability and trustworthiness of tapered bolts.
Industry experts recommend prioritizing the correct specification of tapered bolts for projects. Engineers must account for the load requirements, environmental factors, and material compatibility to achieve the best results. Tools like finite element analysis (FEA) allow for virtual testing of these components under simulated conditions, helping in preemptively identifying potential stress points and mitigating risks associated with bolt failure.
Furthermore, installation techniques play a significant role in the performance of tapered bolts. Proper torque application is crucial as over or under-tightening can lead to premature failure. Training workers in correct installation procedures and the use of torque wrenches calibrated for tapered bolts can prevent such occurrences, ensuring the structural elements they bind remain dependable.
In conclusion, tapered bolts represent a confluence of engineering ingenuity and manufacturing prowess. Their role in ensuring the safety and durability of mechanical assemblies and structures is irrefutable, as is their potential to provide innovative solutions to complex engineering challenges. Bolstering projects with the unmatched stability of tapered bolts not only enhances performance but also prolongs the life of the structures they support, making them an essential part of any engineer's toolkit. As industries continue to demand more advanced and reliable fastening systems, tapered bolts remain at the forefront, backed by their proven track record and continued advancements in material sciences and manufacturing techniques.