Stud bolts, a crucial element in the realm of fastening solutions, serve as indispensable components in various industrial applications, particularly in scenarios where strength, reliability, and precision are paramount. As an experienced professional in the field, I’ve witnessed firsthand the transformative impact that high-quality stud bolts can have on project outcomes. With a profound understanding of their material properties, applications, and maintenance, we can elevate both the effectiveness and longevity of the systems they support.
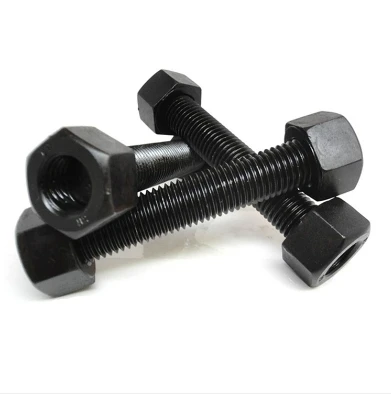
Stud bolts are typically used to join flanges or pipe work within industries such as oil and gas, petrochemical, and power generation.
The key to their effectiveness lies in their design and material composition. Manufactured from high-grade alloys, often carbon steel, stainless steel, or exotic alloys like Inconel or Monel, these bolts offer remarkable strength, resistance to corrosion, and temperature stability. Selecting the appropriate material is critical, depending on the environmental conditions and operational stresses they will face.
From a technical perspective, the installation of stud bolts demands meticulous attention to detail. Torque specifications are crucial; they ensure that the bolt will withstand operational pressures without succumbing to fatigue over time. Installing the bolt with inadequate torque might result in catastrophic failures, while excessive torque can weaken the bolt or even damage the flange. Employing calibrated torque wrenches and strictly adhering to manufacturer guidelines ensures optimal performance and safety.
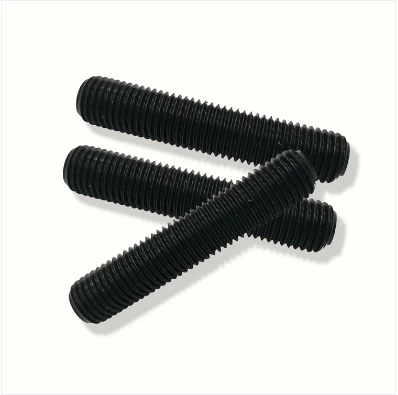
Beyond the realm of mechanics, the concept of traceability in stud bolt production cannot be overstated. Each bolt should be accompanied by a Material Test Report (MTR), verifying its chemistry and mechanical properties. This brings us to another crucial facet procurement from reputable manufacturers. Such manufacturers adhere to stringent industrial standards like ASTM, ASME, or API, guaranteeing the bolts’ quality and compliance.
stud bolt
Regular inspections and maintenance form the backbone of stud bolt performance over time. Corrosion, often the nemesis of any fastener, can be mitigated through protective coatings such as galvanization or PTFE, which provide an additional defensive layer against environmental aggressors. Periodic checks for signs of wear or corrosion, especially in high-stress environments, play a pivotal role in preempting potential failures.
Trust in stud bolt performance is not merely about material and manufacture; it's about installation and maintenance practices too. Utilising a certified installation team ensures that each step of the application process enforces the bolt’s function. Furthermore, continuous training of personnel on the latest techniques and technological advancements fosters an environment where expertise is constantly enhanced.
From academia to industry, publications and guidelines reflect the criticality of this hardware. ASME’s guidelines on pressure vessel design, for instance, underscore the importance of fastener integrity in ensuring system safety and efficiency. Leveraging authoritative resources when planning and executing installation projects leverages this wealth of collective knowledge.
In summation, while stud bolts may appear as humble components in the larger mechanics of industrial projects, their significance is far-reaching. Implementing a strategy that encompasses the selection, precise installation, regular maintenance, and proper training ensures these components contribute effectively to the broader infrastructure. Hence, approaching stud bolts with an understanding of their nuanced demands sets the foundation for industrial successes, reinforcing the bridge between mere components and monumental achievements.